Artisanal manufacturing methods

Artisanal ceramics, methods practiced in the workshop
Clay can be worked in several ways, including casting, modeling and working on a potter's wheel. Depending on the desired result, we will choose one or the other of the proposed techniques.
In my workshop, I practice two approaches to produce my ceramics: modeling and the potter's wheel . These are two distinct land working techniques that offer many possibilities.
Modeling: footed bowl, salad bowl, flat vase, plate, strainer, incense holder, soap dish, trays
Potter's wheel: mug, vase, bowl, flowerpot, soliflore.
Manufacturing Steps:
Creation of the part • drying • 1st Cooking • enamelling • 2nd cooking • Sanding • At your place

Why modeling?
I like the irregular and organic look of this method. I leave room for randomness in the cutting of my trays or on the edges of my salad bowls for example. This accentuates the uniqueness of each of my creations.
There are several ways to approach modeling, we will find the coil method, pinching or even plate work. It is this last technique that I use.
The clay plate
This approach provides a consistent thickness. I combine the clay plates together to create geometric shapes such as my flat vases. Or, I use plaster molds to stamp my clay plate on it to give it the desired shape, we will find footed bowls, salad bowls, colanders...
This method is very slow and allows small daily productions. You can use a plaster mold once or twice a day, after which it is too waterlogged and needs to dry (variable conditions). This involves producing only one or two pieces per day. (I have several molds so I can produce more).

Why the potter's wheel?
I like working on the potter's wheel for the feeling it gives. But also this method allows for “faster” manufacturing, a sort of assembly line work. We obtain mini productions more quickly unlike plaster molds.
The steps of the potter's wheel
First, I prepare some soil. The clay needs to be worked to be homogeneous and free of air. I then weigh my clay to have a regular quantity of material that corresponds to the size of the desired piece. Once this step is finished, I move on to the turn.
During the first day, I turn the pieces. After a drying time which varies with the weather, I come back the next day to work on the back of the piece. This step is called turning. Then I let the pieces dry quietly.
After manufacturing, the first cooking
Once the piece is created, we wait until it is completely dry before putting it in the oven. The first firing, also called biscuit firing, allows the piece to completely evaporate while leaving it porous to be able to apply the enamel. The pieces are fired for the first time at 950°C.

The mesh
I produce my own enamels, this allows me to control the quality and intensity of the colors for a shiny, food-safe and durable finish. My enamels are lead free. This is a manufacturing time to take into account. Mixing each powder is a complex art.
You can learn more here in my blog posts.
I glaze my pieces one by one with well-defined colors. The mixing and layering of enamels brings singularity to each piece when melting them in the kiln.
Final cooking
I then carry out the second cooking at 1250°C. After the last firing, the visible part of the earth is sanded for a soft and pleasant to the touch finish.
Note : Each item is a unique handmade piece, so the shape and color intensity may vary slightly.

Want to learn more about me?
Write me an email to ask me your questions:
Discover my blog with several subjects such as : crafts and ceramics, practical advice, gift ideas, workshop news, glazing research, entrepreneurship. It's a real pleasure of sharing knowledge.
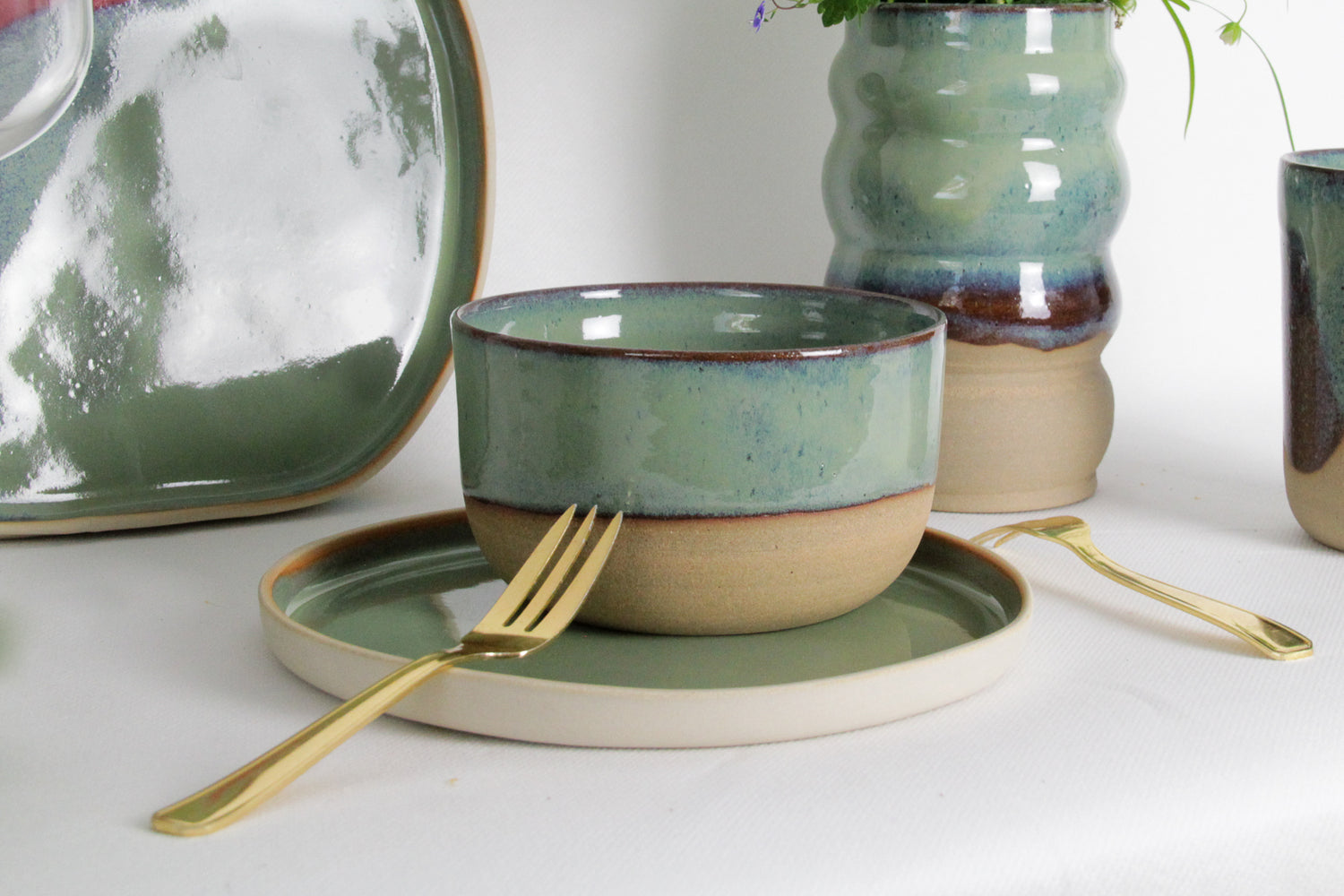
Stay connected on social media to follow my studio life and new creations
-
Handmade in France
All ceramics are made in France in my workshop. The artisanal process extends to the colors. Glazes are developed in my atelier.
-
Daily use
Shock-resistant, ceramics are crafted for a daily-use base. And to provide a nice dose of color.
-
✓ Dishwasher safe
All tableware products are made out of stoneware. Durable and waterproof material. All ceramics are dishwasher safe.
-
Made with love
Ceramics to bring colour, joy and vibrancy to your everyday life!